How do we make milk bottles? And which machine we use?
1) HDPE Raw Material
2) Milk bottle Making Machine
The machine types making milk bottles is depended on the bottle size. We have to know the width, the length and the weight of the bottle to choose suitable machines.
The following are the common machine types making milk bottles.
Machine model | HTSII-3L/6 | HTII-6L/6 | HTSII-8L/8 |
---|---|---|---|
Volume range | 100-500ml | 500ml-1L | 200ml-1L |
Central distance | 70mm | 90mm | 100mm |
Die-head | Six | Six | Eight |
The max. Width of the bottle | 50mm | 70mm | 80mm |
Automatic deflashing | YES | YES | YES |
Capacity (pc/hr) | 2700 -3600 pcs/hr | 2700 -3600 pcs/hr | 3600-4200 pcs/hr |
Your Operator Staff how to start:
What kind of milk bottle making machines do you need?
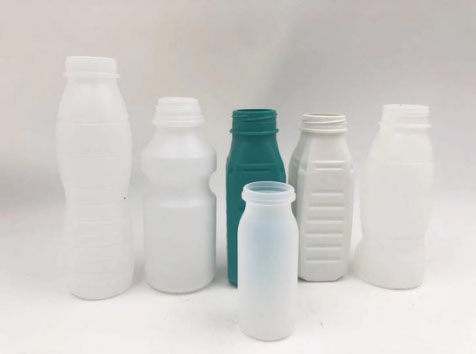
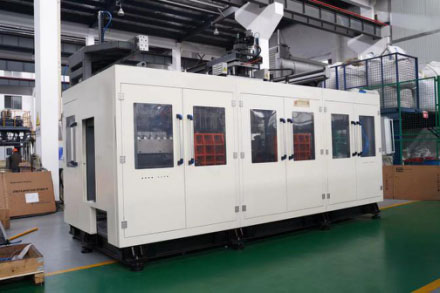
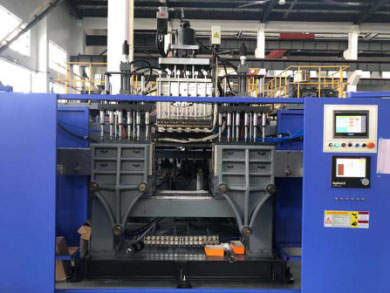
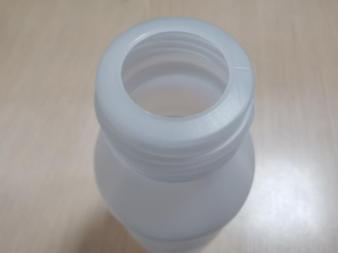
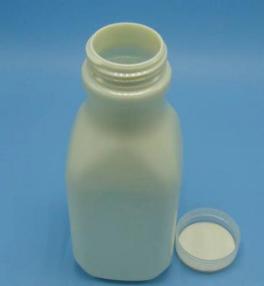
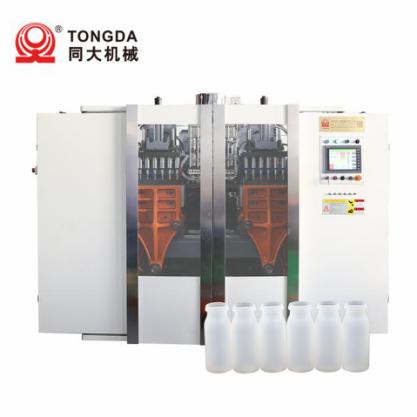
It has advantages as follow: strong clamping force,mold movement fast and stable,clamping force uniform, long mold plate life-span.Scientific template design hole position suitable for a variety of mold installation.
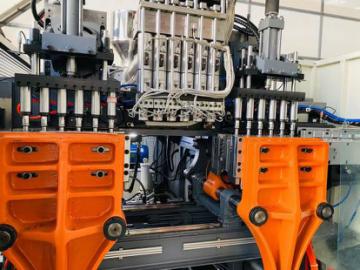
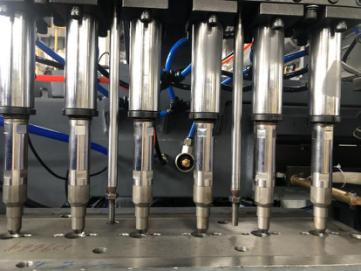
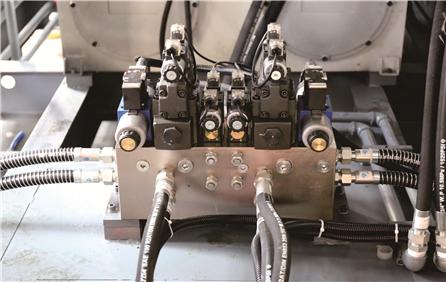
When do you need the robot?
If you want to equip conveyors to connect to the following equipment, such as leak-tester, labeling machine, filling machine, ect. We suggest you to equip take out device to take the milk bottles onto the conveyors.
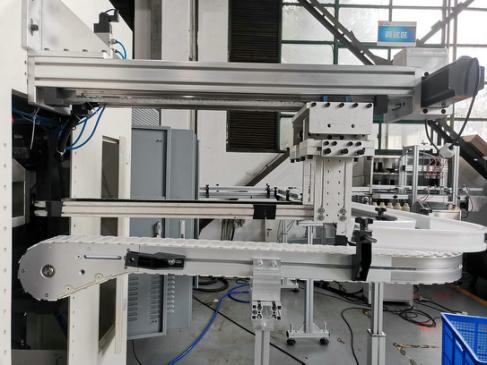
How to find a reliable supplier when you are ready to buy machines?
1)Confirm whether the supplier has its own factory or trading company. Generally speaking, suppliers with their own factories are more reliable.
2)Learn the hard power of the factory, including floor area, registered capital, qualification, processing capacity, manufacturing capacity, etc;
3)Learn the soft power of the factory, including company culture, personnel allocation, technical research and development strength, service ability, etc;
4)Ask supplier provide relevant product videos and customer cases for reference.
5)Discuss project details with suppliers in detail and judge whether the supplier is professional through communication.
6)To learn the position and situation of the company in the industry through domestic friends or peer friends;
7)Through the video call, watch the factory live, understand the actual operation.
8)If conditions permit, visit the factory and judge the actual situation and professional level of the factory through field investigation and face-to-face communication.
Zhangjiagang City is one of the important regions for plastic machinery manufacturing in China, especially with strong strength in extrusion blow moulding machines. Here are many large and small manufacturers. When you are ready to buy a blow molding machine to make milk bottles, you may be confused and don’t know how to find a professional and reliable supplier. In the following we would like to share a few tips for you. As you know, a professional and qualified extrusion blow moulding machine has nearly 1000 small parts inside it, and it is difficult for you to be familiar with all parts. It is not necessary for you to know all of them. You just need to pay attention to some important parts of the blow moulding machine as follow:
4.1 Extrusion & Die System
The biggest and important parts for the single screw extruder are the gearbox, screw and barrel, driving motor, and electrics.
Gearbox: We only use KEWEI brand gearbox for single screw extruder which is a top brand in China. You can find the brand name and picture of gearbox here:
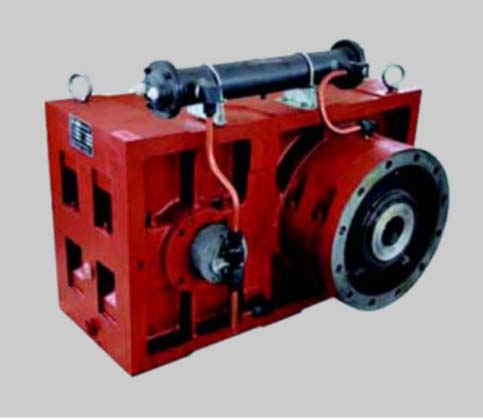
Screw and barrel: The performance of the screw determines the productivity, plasticization quality, dispersion of additives, melt temperature, power consumption, etc. of an extruder, which directly affects the scope of application and production efficiency of the extruder. Through the rotation of the screw, the plastic can be squeezed so that the plastic can move, pressurize and obtain some heat from friction in the barrel. The plastic is mixed and plasticized during the movement of the barrel, and the viscous fluid is melted. When the body is extruded and flows through the die, it obtains the desired shape and is formed. Like the barrel, the screw is made of high-strength, heat-resistant and corrosion-resistant alloy steel. The most common screw diameter is 45-150mm. As the screw diameter increases, the production efficiency of the extruder is also significantly improved. The ratio of the effective length to the diameter of the working part of the screw is referred to as the length-to-diameter ratio, usually 10 to 42. When the length-to-diameter ratio is large, the temperature distribution of the material can be improved, which is conducive to the mixing and plasticization of plastics, and can reduce leakage and reverse flow, and improve the production capacity of the extruder.
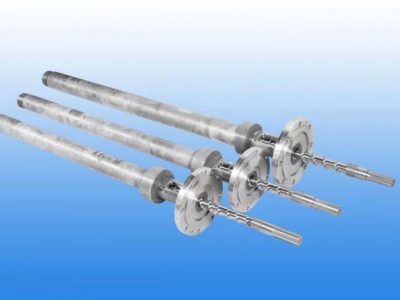
What we also need to know is the process of its surface, whether they are bi-metallic or Polymer screw. The cost of Polymer screw processing is higher than bi-metallic. Polymer screw processing is suitable for your use.
Driving Motor: SIEMENS brand is our prior choice, and it is AC type, but you should know that all Siemens brand is made in China.
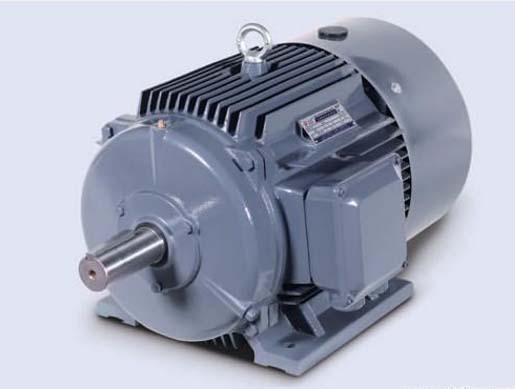
Electrics: These are the brands of electric devices that we use in production, but you can also compare these with other brands.
Name | Supplier |
---|---|
Microcomputer Control System | MITSUBISHI PLC, Japan |
Touch Screen | INNOVANCE,CHINA |
Parison Controller | MOOG ,Japan or AUTOMATA,GERMANY |
Contactor | SCHNEIDER, France |
Air Switch | SCHNEIDER, France |
Motor | SIMENS BEIDE, Germany |
Power Resource | MEAN WELL, Taiwan |
Inverter | INOVANCE |
Relay | OMRON, Japan |
Transducer | GERMANJET, GermanyOR GEFRAN, Italy |
Solid state relay | ARICO, Taiwan |
Servo valve | Rexroth,Germany |
Servo pump | Sumitomo,Japan |
As you know that plastic extrusion blow molding machines is supposed to work non-stop in your plant, electric parts are very easy to be damaged if the quality is not good. You can find electric parts from international manufacturers in your market, but prices would be much higher than those in the Chinese market. We always recommend opting for our after-sales service, because you can also find counterfeit products in your local market. Anyway, we only need to know what brand they use in their machine when you are visiting plastic extrusion blow molding machines manufacturing factories in China.
4.2 Die Head
The die head is the forming part of the extrusion machine, which mainly includes the head, mandrel, die mouth, core model, adjusting screw, etc. The die head is connected with the extruder. The extruder provides a plasticized plastic melt with a certain temperature, pressure, viscosity, and runner speed for the die. After the plastic melt enters the die, the original spiral motion mode is changed to the linear motion mode. The flow and shear process of the melt in the runner makes the plastic melt further uniform. The melt is decompressed in the flow channel to make the speed uniform, and the melt is further compressed and pressurized to generate the necessary molding pressure to make the extruded product compact. Finally, the melt undergoes the forming section of the die to become a parison with a certain cross-sectional shape and size, and the parison is then processed and cooled to form a product. Die heads have multiple forms of single-layer, double-layer, multi-layer, and single-die, double-die, and multi-die.
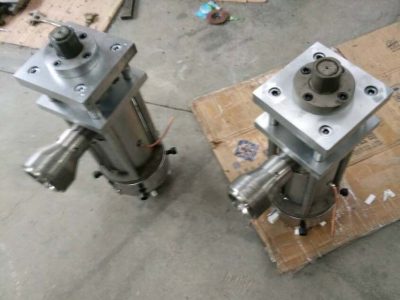
For plastic extruding die head, you would need to use it several times to know its quality. A good blow molding machine die head has better rheological properties, which can make the plastic melt have a better preform structure, and at the same time, it is easier to change the material and color of the plastic material.
4.3 Control System
Human-machine interface: Human-machine interface control panel screen has such functions as follow: visual display providing the best support to easily set, search, change and store the parameters, the controlling system has self-diagnosis, functions, the malfunctions can be displayed on the screen. Now we usually adopt INOVANCE brand.
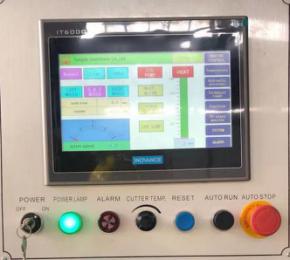
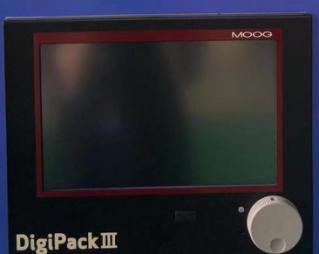
4.5 Hydraulic System: Hydraulic controlling system uses servo-controlled technology to control the movements of actuators and all the elements used in hydraulic system are famous brands such as Japan YUKEN, it has advantages as follow: quick response and high energy-efficiency. Optional hydraulic system could save about 50% energy.
What auxiliary machines you need whenenen buying jerry can making machine.
1.Auto-loader
Loader is used to feed the material to the hopper. It helps save labor from carrying materials. By blocking the transport system, it improves the workshop environment, reduce pollution and ambient temperature. When choose auto-loader, as most jerry cans are 1 liters, 4liters and 5 liters, and the weight usually won’t over 250g, so 400kg/hour is enough.
2.Chiller
Cooling water is mostly used to cool the mold. (1) If the mold to hot, it is not easy to molding the products. (2) Facilitate the demold, then the jerry can won’t stick to the mold. (3) Decrease the time high pressure inflate, after that the cycle time can be faster.
3.Mixer
Mixer are used to mix up raw material and color master batch to make the jerry can have attractive colors. Or it can mix up virgin material and recycled material, helping save cost of materials. Control box sends signal to the motor, and it starts rotating. Motor main shaft drives blades to mix different materials with the rotation, which evenly mix the material in short cycle. When timer of the control box reaches set time, the motor stops. At this time, open the discharge port of the hopper, and discharge the material. Then, the mixing is finished.
4.Crusher
During processing progress, there will be waste material or some failed jerry cans. Crusher is suitable for granulating plastic material. The waste materials enter the cutting chamber via material inlet (A). The rotary blade (B) and fixed blade (C) granulate the materials. The particle size is controlled by the size of screen (D). The screen (D) is located at the bottom of cutting chamber. Thus it is convenient to replace screen to other different sizes.The granulated materials are dropped into the storage box (E) via the screen and be conveyed via discharging pipe (F). Use feeding blower to absorb the granulated materials into cyclone dust collector to separate the air and dust. The particles can be reused directly or sent to somewhere for storage after being granulated.
5.Air compressor
We usually supply customers with a set of air compressor which consists of air dryer, filter and air tank. Many functions need compressed air, such as high pressure inflate, deflashing, cutter and so on.
There are still many other auxiliary engines that improve the automation of your company, helps save labor and increase the production efficiency.
What do you need to prepare before getting the jerry can manufacturing machine?
First of all, you have to conform the area you need for your plant. After the machines arriving at your factory, the first step is to install the legs and adjust the balance of them. Also, you need to tighten all the screws, as the screws may loose during the long-time transport. Besides, the necessary things you need in your factory are water, electricity, gas and hydraulic oil.
6.1 Water
The water source can be a cooling pool pump system, also can be adopted according to the requirement of the finished products. The mold uses cooling water or all the system can also use cooling water from chiller.
If you have several machines, it is better for you to build a water pool to store water in your factory. The function of the water pool is the same as the water tower. Also, you need to connect the water chiller, as the water temperature of the water pool is not low enough to cool the mold.
The functions of the water are as follows:
To cool the mold
If the temperature of the mold is too high, the product will be deformed.
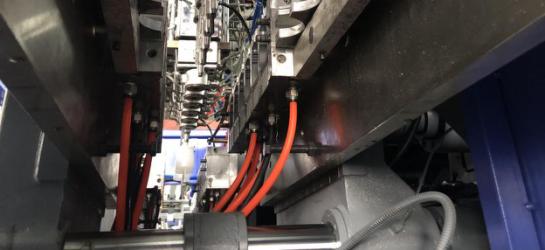
To cool the die head: If there is no water cooling on the die head, the sealing rings on the Servo cylinder may broken for the high temperature.
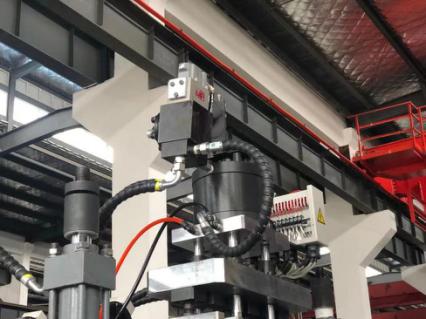
To cool the blow pin: If the temperature of the blow pin is too high, the product mouth size will get small.
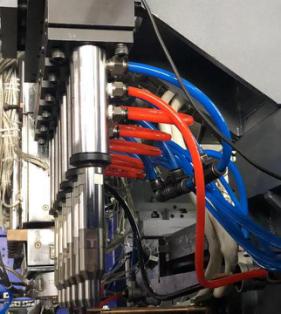
To cool the screw: If you didn’t connect the water in the material inlet part, the temperature in the front of the screw passes to the back, the material will agglomerate.
To cool the oil tank: There is a water cooler outside the oil tank.
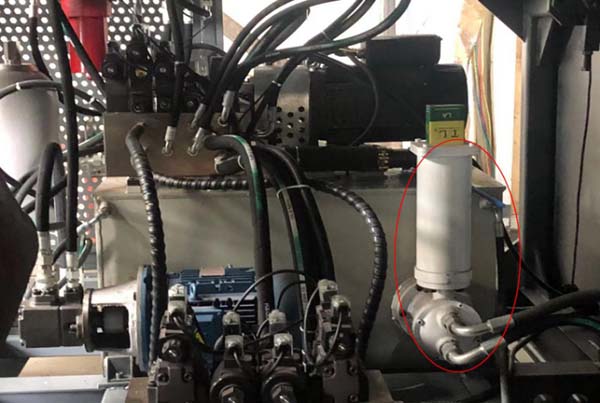
6.2 Electricity
You can refer to the manual to know the total power needed to run the machine. Before you get a quotation from us, we also need to know the voltage and frequency of your country. When removing the electrical box before shipment, we will mark the number on the wires. It will be easier for you to connect all the wires. The grounding place will be better if close to the machine. If not grounded well, starting the machine is strictly prohibited.
6.3 Gas
You have to prepare the air tank and air compressor to provide the gas. Make sure the total air source pressure gauge reaches to 0.6. The pressure reducing valve reaches to 0.2.
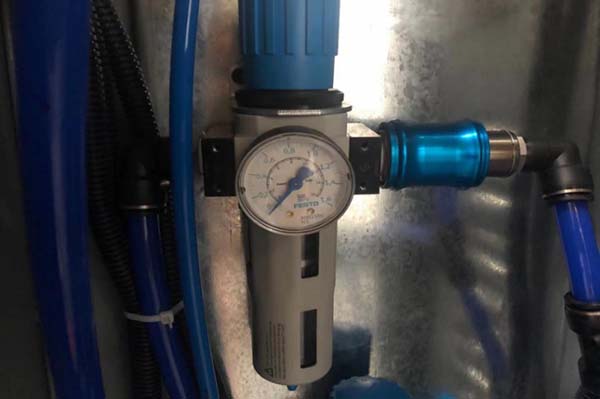
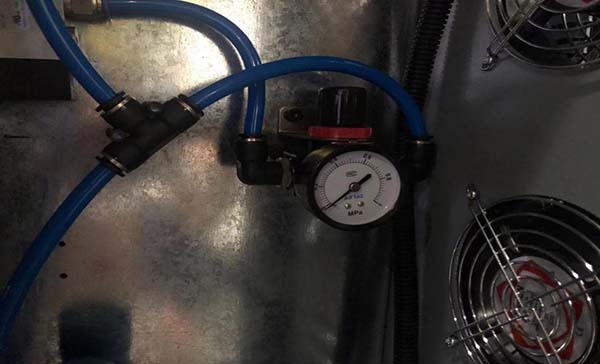
The total air source controls all the gas output. The pressure reducing valve is used for stabling
air volume output used for actions, such as cutter output, deflashing output, die head blowing, blow pin, taking out arms.
6.4Hydraulic oil
Before operating the new machine, please fill the hydraulic oil into the oil tank.
Open the filter of the oil tank to fill in hydraulic oil N46# (when the environmental temperature is high) or N32# (when the environmental temperature is low). Check the oil level from view window on the side of oil tank, the oil level should be between Max. limitation and Min. limitation.
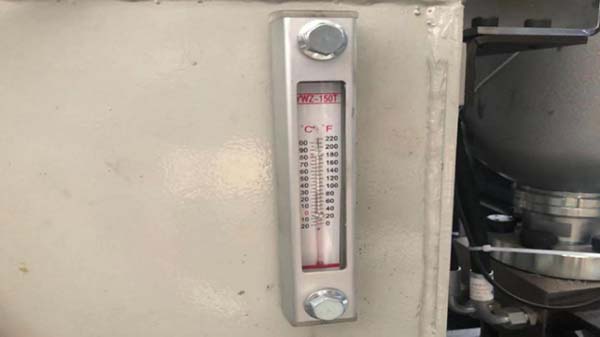