TONGDA MACHINERY
HT-2L
Products Description

Product Application
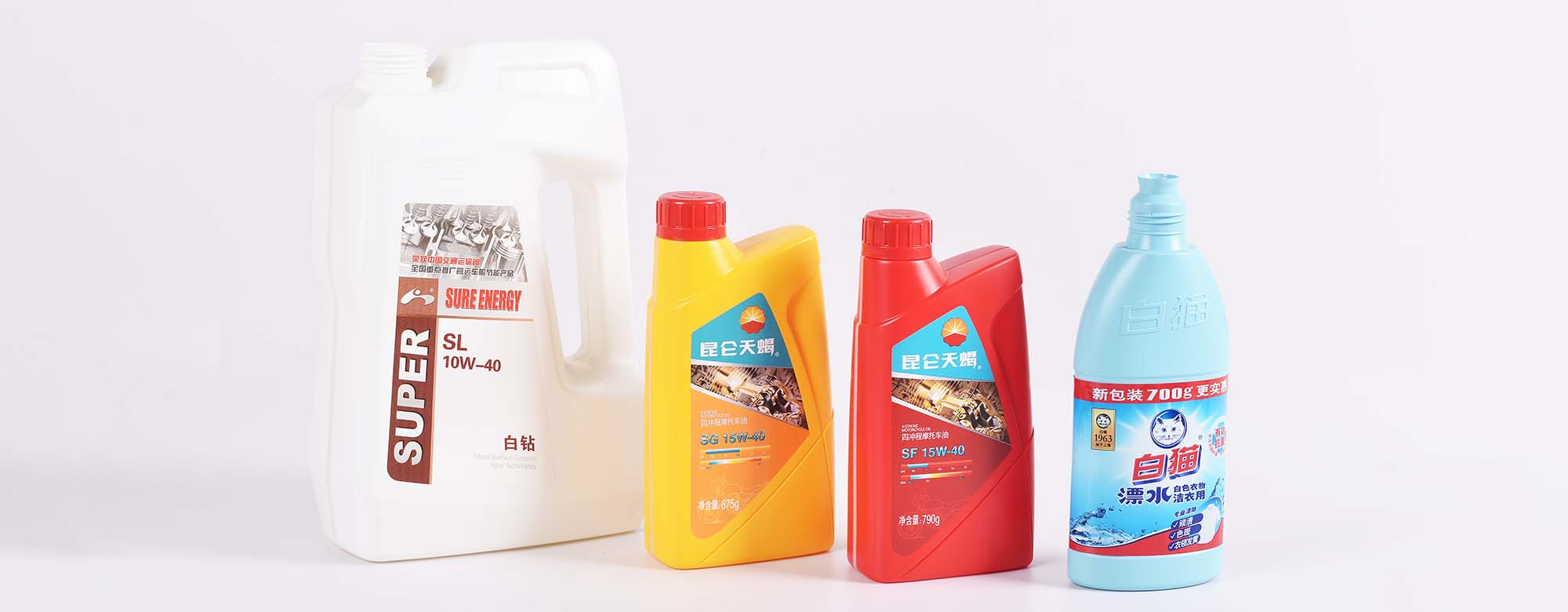

Machine Details
Clamping unit, blow pin unit
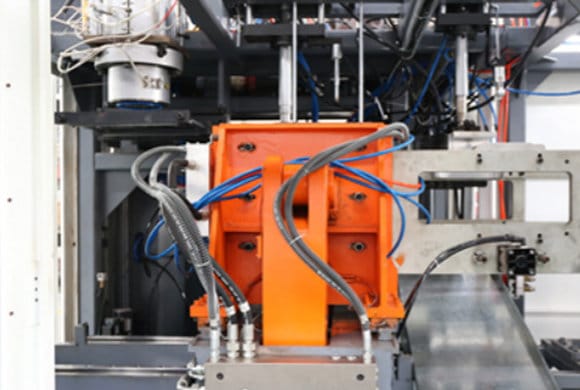
Strong clamping force, mold movement fast and stable, clamping force uniform, long mold plate lifespan. Scientific template design hole position suitable for a variety of mold installation.
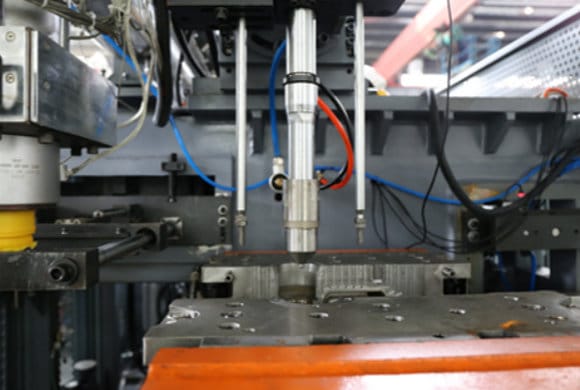
Up blow needle suit (single head to muti head) , suitable continous head machine. Blow pin design suitable, it can realize better cooling and cycle blowing air.
Electric system & hydraulic system
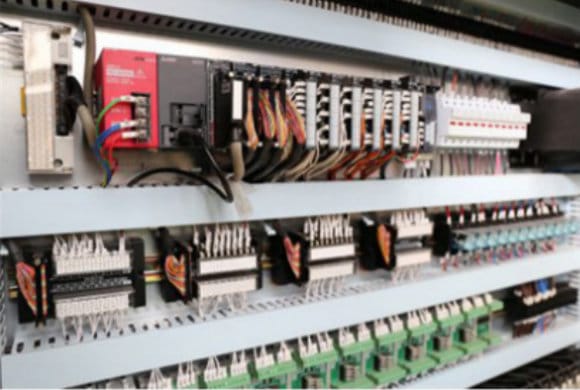
Mitsubishi PLCsystem and humanmachine interface control (Chinese & English language ). Touch screen operation. Setting parameters, changing parameters, searching, monitoring,fault diagnosis and other functions are done by the touch screen.
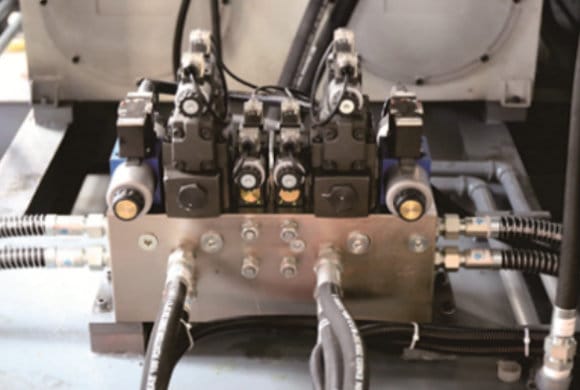
Hydraulic controlling system uses servo-controlled technologyto control the movements of actuators and all the elementsused in hydraulic system are famous brands, it has advantages as follow: quick response and high energy-efficiency. Optional hydraulic system could save about 50% energy.

Other Advantages
Suzhou Tongda Machinery Co., Ltd. is located in Zhangjiagang City, Fenghuang town Korea Industrial Park. 2 hours away from Shanghai City by car. In the recent 20 years, Suzhou Tongda Machinery Co., Ltd. has been focusing on the research, development and product application of extrusion blow molding machines. The factory covers an area of more than 80 acres of land and has more than 270 employees. The company has established Engineering Technology Research and Development Center, and Jiangsu Province excellent Graduate work Jiangsu Enterprise Research and Development Center, Jiangsu Province Extrusion blow Molding Technology Technology Center has more than 50 R & D personnel, including 1 national science and technology talent, Station. Jiangsu Province post-doctoral innovation practice base and other R & D platforms, at present, the that means constantly exploring the expansion of new areas. Warmly welcome new and old customers to visit, to guide, 4 senior masters,15 bachelors, hosting the development of two national standards and participating in the formulation of a national standard. “Working Together to Grow Together” is the spirit of TONGDA company, to cooperate with us and we are always at your service to provide you with strong support.
Under normal conditions,the blow molding machine to abroad will be packaged in wooden case. ln addition,we will also pack the machine according to the requirements of specific customers.Subject to the measurement of main blower, we will choose corresponding wooden case, TONGDA is a professional blow molding machinery company we will try our best to satisfy the kinds of demand of customers.
Service Marketing Network
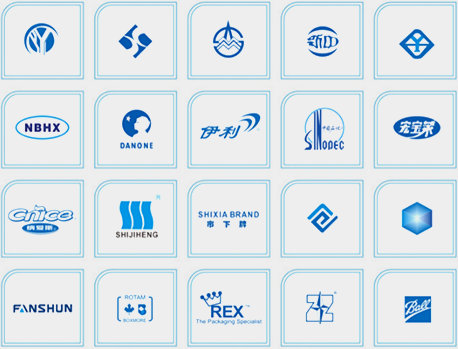

FAQ
First of all, ensure that the tube blank is straightened forward and backward, and then adjust the two adjustment screws behind the die.
1) Whether the die blast is too large, reduce the die blast;
2) The mold temperature is too low and the mold temperature needs to be increased;
3) The mold exhaust is not enough, and the mold exhaust is needed.
1) If the pressure is too small, increase the clamping pressure;
2) The mold overflow groove is too shallow, deepen the mold overflow groove;
3) The mold is not flat, adjust the mold to make it flat;
4) The template is not flat, adjust the template to make it flat.
1) The clamping speed is too fast. Adjust the process time and close the mold slowly.
2) The knife edge of the mold is too sharp or has burrs, repair the knife edge.
3) The shape of the mold handle is unreasonable, and the details of the process are not considered in the design.
4) The die is too small or the die blast is too small. Enlarge the die or adjust the blasting process.
5) The tube embryo is not round enough and has wrinkles. Remake the die and increase the pressure of the die.
6) The mold temperature is too high, the material will be broken when the mold is closed. The mold temperature is controlled by cooling water and chiller.
7) For products with in-mold blowing handles:
①The blowing needle in the mold is short or the time of blowing needle is too early or too late.
②The design of the blowing needle cylinder in the mold is unreasonable. There are two types of cylinders, one is blowing while tying, only one action, which is not stable enough. The other is to pierce and blow, which is relatively stable, but has certain requirements for the machine itself, and the mold opening and closing stroke needs to be larger.
1) Adjust the corresponding wall thickness (but the effect is not very good)
2) Corresponding four-corner die trimming, because the material comes out of the die is a blank with uniform wall thickness, for a square product with four corners stretched larger, it needs to be placed at the corresponding four corners of the die Wear some, usually to repair the mold sleeve, and the segmented mold core can be repaired.
1) The cutter did not cut the material, and the mouth of the bottle did not open when the blowing needle went down, causing material to be carried. Solution:
① Observe whether the blade is blunt or damaged.
② Observe whether the screws fixing the blade are loose.
③Sometimes it has a certain relationship with die bulging and often blowing。
2) The size of the blow needle is wrong, and the blow needle size needs to be modified.
3) The angle of the mold knife edge is wrong or the diameter is too small, and the mold knife edge needs to be modified.
4) The process time is set incorrectly, adjust the pre-blowing time and the lower speed of the blowing needle.
The liquid level lines commonly used by our company are generally Φ22 and Φ30.
Φ22 is installed on the die head.
Φ30 is installed on the plasticizing system.
It can be installed later.
For a single die head machine, change the die head body, install a penetrating ring, add a throttle plug and throttle plug seat, and install an extrusion system.
For a multi-die machine, the die body, penetrating ring, throttle plug and throttle plug seat need to be multiplied by the corresponding number of die heads.
Yes.
For some wide bottle mouths, larger diameter jars, and products that need to be plastic-sealed again in the later period, we recommend that you choose a rotary cut mouth.